The Indian pharmaceutical industry thrives on a network of PCD (Propaganda and Distribution) pharma franchises. These partnerships allow established pharmaceutical companies to expand their reach through a network of distributors. However, in this fast-paced and competitive market, success hinges not just on brand recognition and marketing prowess, but also on an unwavering commitment to quality control (QC). This blog post, brought to you by Rowlinges Lifesciences, a leading PCD pharma franchise company, delves into the critical role QC plays in ensuring the viability and success of PCD pharma franchises.
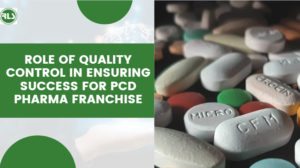
Why Quality Control Matters in PCD Pharma Franchises
In the realm of pharmaceuticals, there’s no room for compromise. Medicines are meant to heal, not harm. Stringent quality control measures are not just a regulatory requirement; they are the cornerstone of patient safety, brand reputation, and ultimately, the success of any PCD pharma franchise. Here’s why:
- Ensuring Patient Safety: Flawed or contaminated medicines can have devastating consequences. Robust QC processes guarantee the safety and efficacy of pharmaceutical products, minimizing the risk of adverse reactions and protecting patient well-being.
- Building Trust with Healthcare Professionals: Doctors and pharmacists rely on the quality and consistency of pharmaceutical products to deliver optimal care to their patients. A reputation for high-quality products fosters trust with healthcare professionals, leading to increased prescription rates and stronger business partnerships.
- Maintaining Brand Reputation: In a competitive market, brand reputation is everything. Consistent adherence to quality standards builds brand recognition and trust amongst consumers, ultimately driving sales and market share for the PCD franchise.
- Reducing Regulatory Risks: Regulatory bodies in India, like the Drugs and Cosmetics Act (DCA) 1 and the Central Drugs Standard Control Organization (CDSCO) 2, enforce strict quality control guidelines. A robust QC system ensures compliance with these regulations, minimizing the risk of penalties and legal repercussions for the franchise.
Key Stages of Quality Control in PCD Pharma Franchises
Quality control is not a one-time event; it’s a continuous process that encompasses all stages of the product lifecycle:
- Raw Material Testing: Before production begins, rigorous testing is conducted on raw materials to ensure their purity, potency, and identity. This helps prevent contamination and ensures only high-quality materials are used in the manufacturing process.
- In-Process Quality Control: Throughout the manufacturing process, regular checks are performed to monitor critical parameters like temperature, pressure, and mixing times. This ensures adherence to established protocols and prevents inconsistencies in the final product.
- Finished Product Testing: Once production is complete, the final product undergoes a series of tests to verify its compliance with predefined specifications. This includes tests for potency, purity, stability, and dissolution rate.
- Stability Testing: Pharmaceutical products degrade over time. Stability testing evaluates how a product maintains its potency and physical characteristics under different storage conditions, ensuring its efficacy throughout its shelf life.
Beyond Regulatory Compliance: Building a Culture of Quality
While adhering to regulatory requirements is essential, a successful PCD pharma franchise fosters a culture of quality that goes beyond mere compliance. This involves:
- Investing in QC Equipment and Infrastructure: Having access to advanced testing equipment and well-maintained laboratories is crucial for conducting thorough quality checks.
- Continuous Staff Training: Regular training programs for QC personnel ensure they stay updated on the latest methodologies and best practices in quality control.
- Maintaining Detailed Documentation: Proper documentation of all QC procedures and test results is vital for traceability and regulatory compliance.
- Encouraging Open Communication: A culture of open communication within the organization allows for the timely identification and rectification of any quality issues.
The Rowlinges Lifesciences Commitment to Quality
At Rowlinges Lifesciences, we understand that quality is the cornerstone of a thriving PCD pharma franchise. We are committed to upholding the highest standards of quality control throughout our entire production process. Here’s what sets us apart:
- State-of-the-Art Manufacturing Facilities: Our facilities are equip with advanced machinery and undergo regular audits to ensure compliance with cGMP (Current Good Manufacturing Practice) guidelines.
- Highly Qualified QC Personnel: Our team comprises experienced professionals dedicated to maintaining the highest quality standards.
- Stringent Testing Procedures: We conduct comprehensive testing at every stage of production, from raw materials to finished products.
- Transparency and Traceability: We maintain meticulous records of all QC procedures and test results, ensuring complete transparency throughout the supply chain.
Conclusion
Quality control is not a cost center; it’s an investment in the future of your PCD pharma franchise. By prioritizing quality at every step, you safeguard patient safety, build trust with healthcare professionals and consumers, and ultimately pave the way for long-term success in the Indian pharmaceutical market.
Contact Information
Name – Rowlinges Lifesciences
Mail – rowlingeslifesciences1@gmail.com
Phone. No – 8283003093, 8288982258
Address – Plot No. 176, Phase-2, Industrial Area, Panchkula (H.R)